Modular Construction
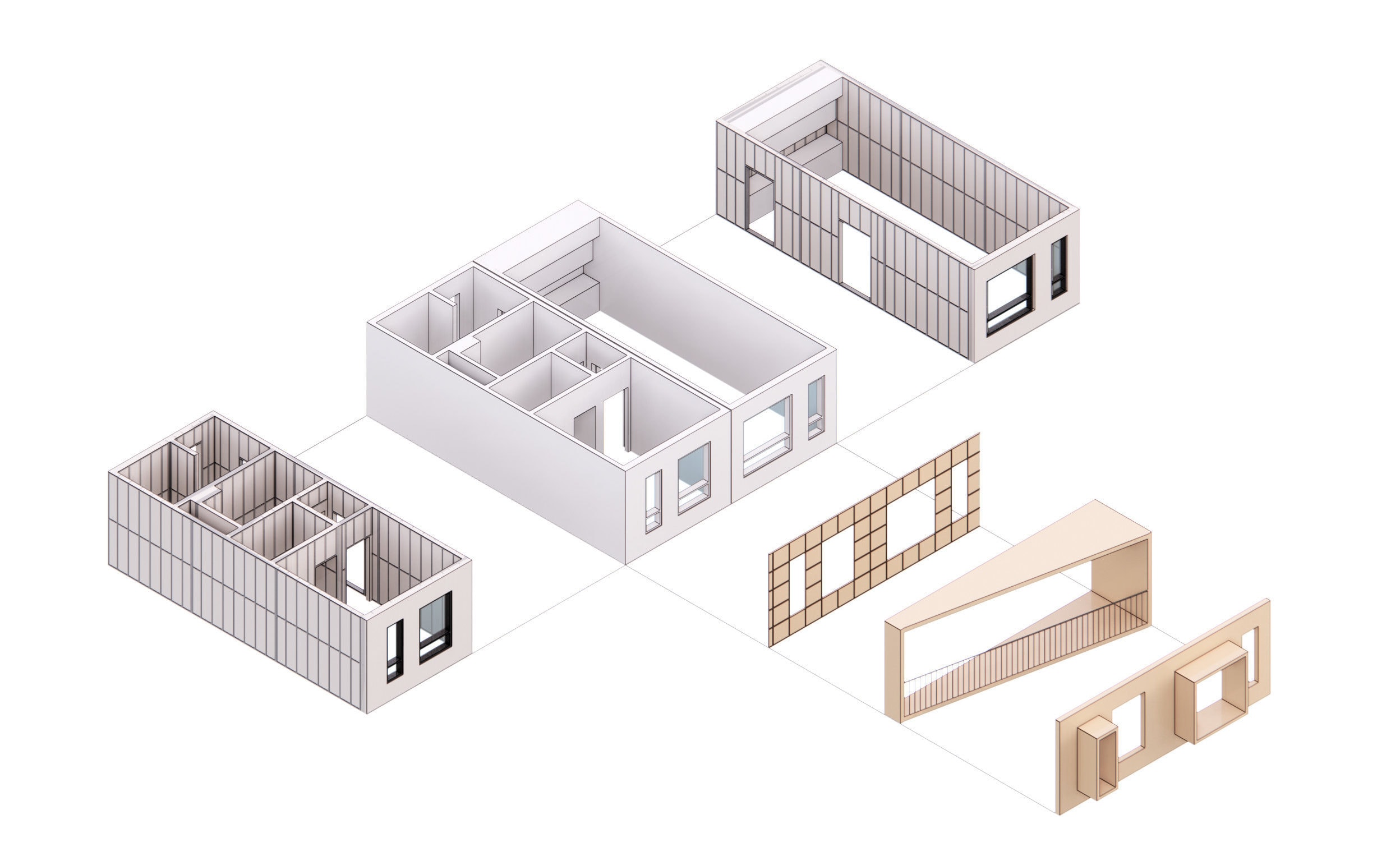
Our housing experts employ best practices to create spaces that enrich the lives of all residents, from students to seniors to mixed-use, intergenerational communities.
Our guiding principle is a holistic approach to housing design – one that is sensitive to the idea of timeless architecture, celebrates human emotion, and creates a unique sense of place. Steinberg Hart has designed housing since the firm’s inception, including affordable, market-rate, and mixed-use. On every project, ranging from high-rise towers to the single-family home, we strive to create a distinct residential experience.
Now, we are applying this expertise to the next generation of housing typologies.
Modular: One major factor in unaffordability in the rental housing market is the rise in construction costs. Rising construction costs can be offset by streamlining the construction and design processes through modular or prefabrication construction.
Most residential or hospitality designs will have repetitive components, which makes them a good fit for modular unit construction. It is possible to provide modular components only, such as for bathrooms. Modular components can provide a high level of design without sacrificing quality, and they can be mocked up well ahead of construction to make any desired changes.
Micro-housing: Micro-housing is a reaction to our increasingly dense cities’ rising housing costs and is a response to a growing desire for affordable downtown living. Defined as units 350 SF or smaller, micro-units are designed to make the most of their reduced living area with highly-rationalized circulation and flexible furniture and spaces. This attracts young professionals who put a premium on vibrant and convenient locations. Micro-housing buildings often offer highly desirable shared amenities and thriving communities to make the buildings’ common areas an extension of their compact living spaces.
Steel modular construction is setting new standards for cost-effectiveness and construction efficiency.
Modular projects condense design, construction, permitting, and delivery. With all phases happening simultaneously, Steinberg Hart’s highly-technical team utilizes the full breadth of digital tools at hand, including 3D Building Information Modeling (BIM) and virtual and augmented reality, to optimize the decision-making process. Further, a complete proof of concept unit was factory-constructed and assembled on site in the heart of Downtown Los Angeles.
These 320 SF micro-units make the most of a tight infill site. We achieved a highly rational, streamlined floor plan, working within the code constraints and the stringent Chapter 11B accessibility requirements to optimize each square inch of the floor plans.
Within the modular system, micro-units generate additional efficiency above the podium level. This ensures that the project can be completed at a significantly lower cost and at a higher level of finish than with traditional wood-frame construction.
60-90% of modular construction occurs off-site. Modular project delivery requires early design and manufacturing coordination, but can provide time savings of 30-50%, as compared to traditional site-built project delivery methods. Modular manufacturing allows for a more controlled environment vs. site-built construction, leading to better precision, safer construction, eliminated weather days, and less waste.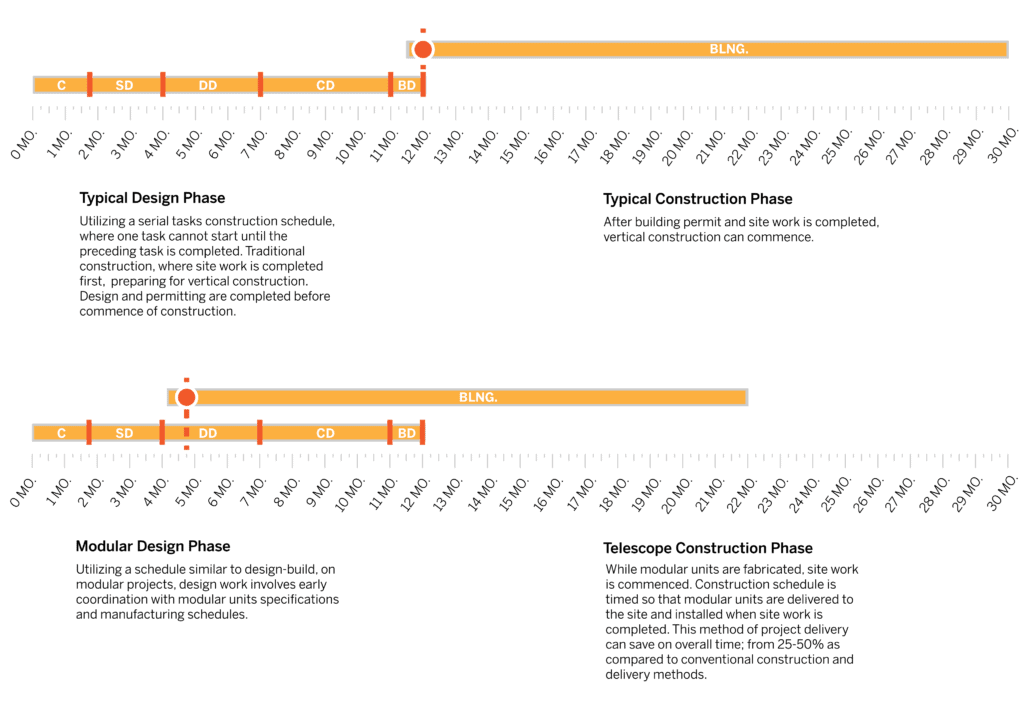
Of great importance is the ability to manage transport of the modules from factory to site. CALTrans requires a special permit for loads wider than 8’-6” and taller than 13’-0”. And, ISO provides standards for shipping container dimensions.
Wood vs. Steel
When comparing wood modular construction to steel, one must consider the following. We know that wood provides superior insulation, and is a structurally sound, sustainable material. It is bio-degradable and recyclable, with low toxin levels. However, wood modular construction is limited to just five stories, which has hindered large-scale adoption. Steel on the other hand, is a rigid, recyclable construction material with durable long-term behavior. Steel modular provides a more air-tight exterior envelope, which allows for gains in energy conservation. And, in addition to providing opportunities for built0in moment frames, steel modular has the unique advantage of unlimited height applications.
It is clear that modular construction, and in particular, steel modular construction, provides a number of unique opportunities.
Below, we have summarized the time, size, and level ranges for each stage of the modular construction process. Steinberg Hart has been working closely with developers and manufacturers to create a viable deployment roadmap for steel modular construction. Today, we have four such modular projects in the design or construction phases.